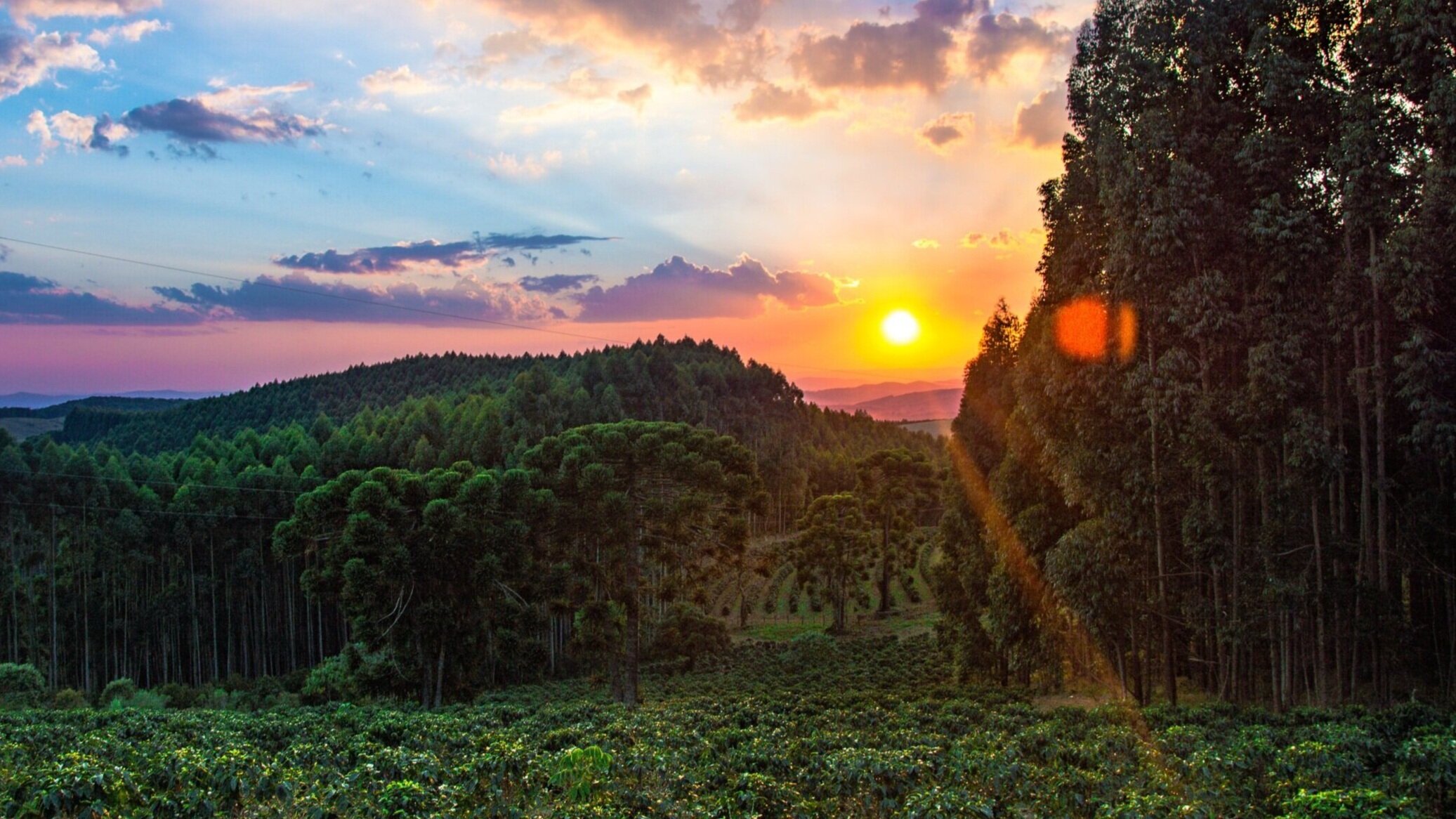
Sustainability
“Sustainability is no longer about doing less harm. It's about doing more good.”
Jochen Zeitz
Apffels Fine Coffee – Carbon Footprint Analysis
California Title 24 building compliance (lighting, Low-e windows, HVAC, insulation).
Ambient lighting in 80% of manufacturing areas via roof skylights reducing high bay
lighting requirements by 40%.Additional roof insulation and interior Insulated Metal Panel walls to manage
production conditioned spaces.State-of-the-art emission controls for roasting operations (catalytic oxidizer):
a. 45% reduction in greenhouse gas emissions versus conventional thermal afterburner (and SCAQMD approved) emission control systems.
b. High-efficiency passive cyclones remove 95% of airborne particulate in convection airstream reducing particulate emissions and burner energy required to destruct.
State of the art re-circulating coffee roasters:
a. Using on average 60% of preheated air during roasting cycle reducing natural gas requirement versus heating ambient air. Equates to a 20% to 30% reduction in greenhouse gas emissions versus conventional single-pass roasters.
b. Cooling air requirements drawn from outside the building reducing the number of required air changes per hour in production areas reducing the energy required to condition space and circulate air by 15%.
c. Extra insulation on hot components reducing the need to condition production areas.
Use of mechanical versus pneumatic conveyance systems reducing electrical power
requirement by 75%.Extensive use of variable frequency drives for electrical motors reducing electrical demand.
Sealed conveyance and storage systems:
a. Reducing nitrogen requirements by 15% resulting in reduced air compressor usage
versus traditional systems.b. Reduces the number of required air changes per hour in production areas reducing the energy required to condition space and circulate air.
Use of water-cooled coffee grinders increasing throughput by 25% with only 10% additional
energy requirements.Installation of high-efficiency lighting system to reduce energy consumption by 25%
Installation of motion sensors to turn lights off and on non-essential work areas.
Paper recycling program.
Corrugate recycling.
Burlap bag recycling.
Donation of scrap coffee to charitable organizations.
Integrated Electrical Management Program, uniquely designed to eliminate “peak” electrical consumption through realigned systems, protocols and new technologies.

Where technology, science, and experience combine to produce exceptional quality and consistent products.